Discover VSM
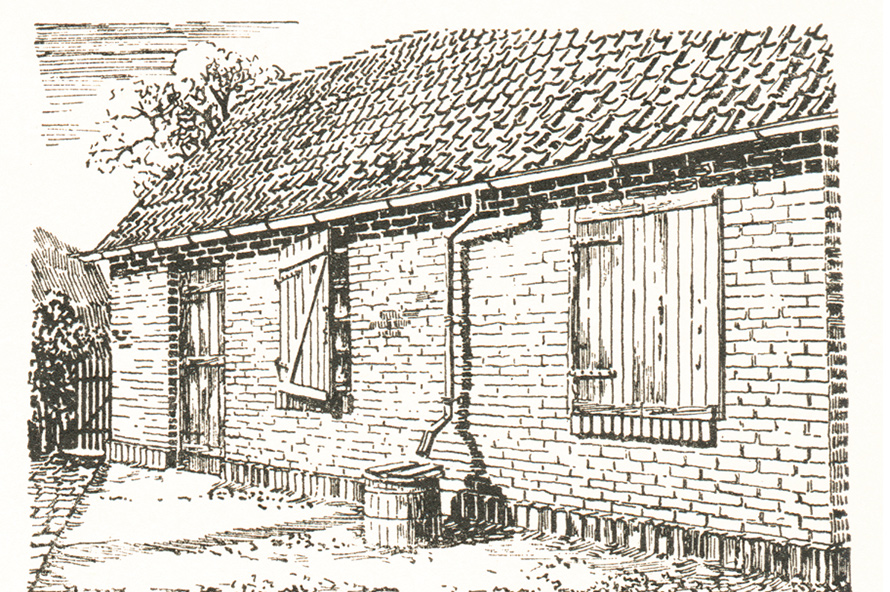
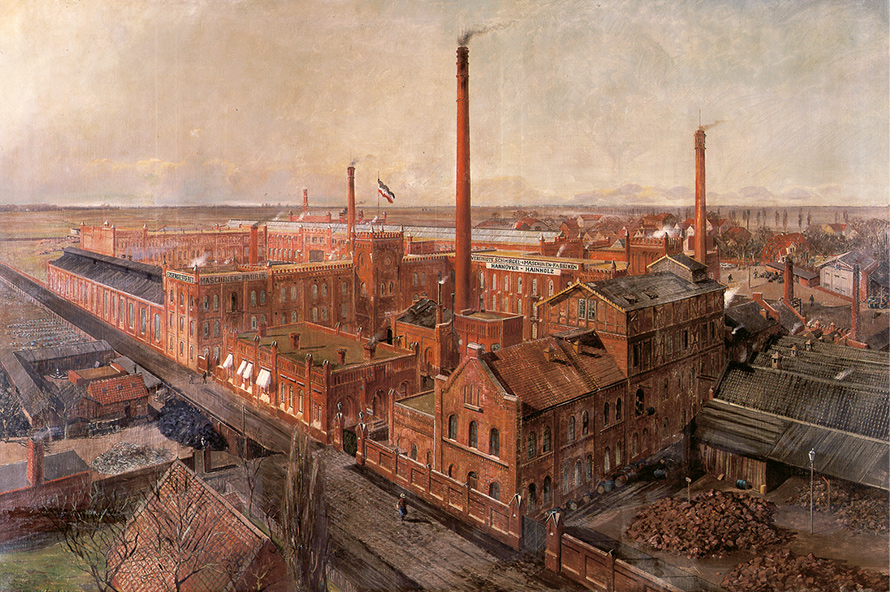
1864: Business start-up
On 28 May 1864, Siegmund Oppenheim and his technically skilled brother-in-law Siegmund Seeligmann laid the foundations of what was later to become VSM. The company named S. Oppenheim & Co. began working in small production rooms in Hanover-Hainholz.
More than 160 years later, VSM's headquarters and production is still at this location. While the company started operations in open countryside in 1864, the city of Hanover has now grown around the plant. This makes VSM one of the few inner-city industrial enterprises in the Lower Saxony state capital of Hanover.
In addition to the location, VSM has also remained loyal to its own products. Back then, small-scale production and manual processes were used to manufacture glass and flint paper. The basic principle applies today as it did back then: A backing is coated with a bonding agent and covered with an abrasive material. Of course, both the materials used and the production processes have changed significantly over the past 160 years.
Today abrasives continue to be VSM's main product.
Discover VSM
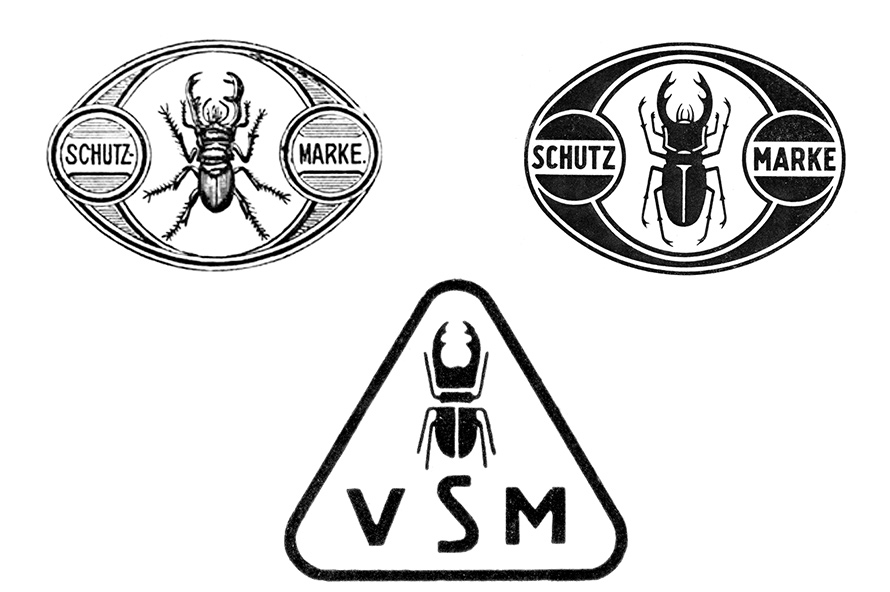
1875: The stag beetle trademark
Walk carefully through the VSM company premises today and you will see it over and over again: The stag beetle. In 1875 it was registered as a trademark by the company S. Oppenheim & Co. Back then, trademark protection law allowed trademarks to be registered with the District Court. The founding fathers of what later became VSM recognised the value of a memorable logo at an early stage. For this reason, they registered the stag beetle as a trademark. It is the largest and most distinctive looking beetle in Europe.
VSM used a range of different versions as a trademark for their natural abrasives. As more and more synthetic abrasives were used in the 1950s, the stag beetle was superseded by the new brand name VITEX.
Discover VSM
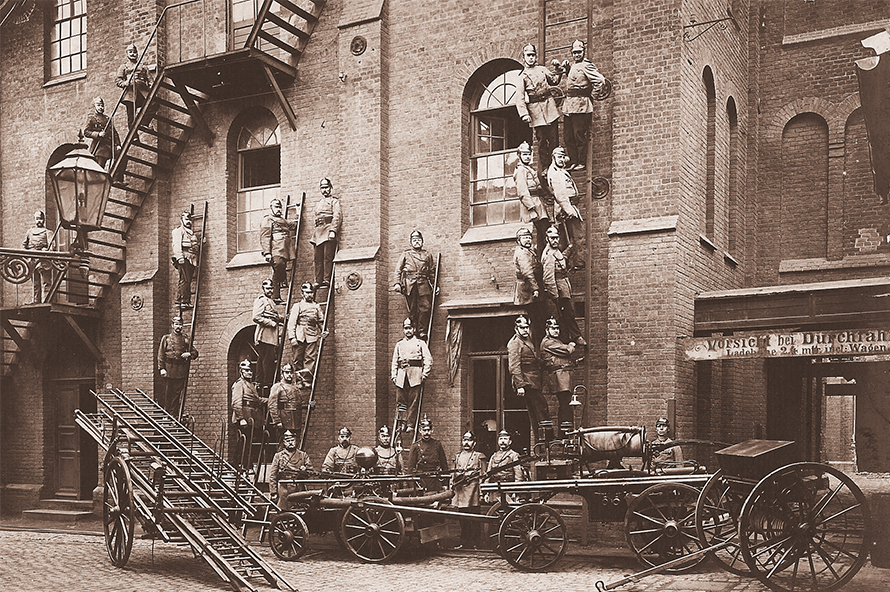
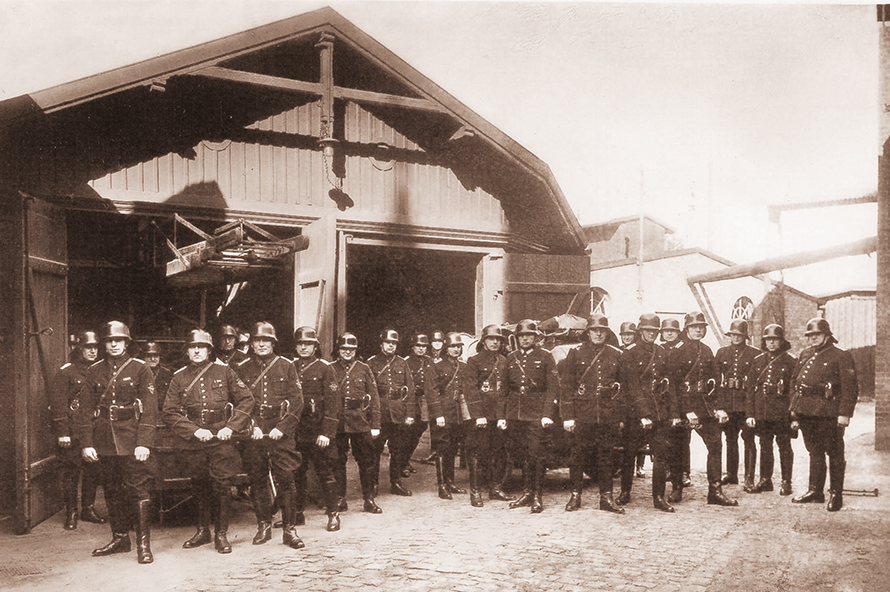
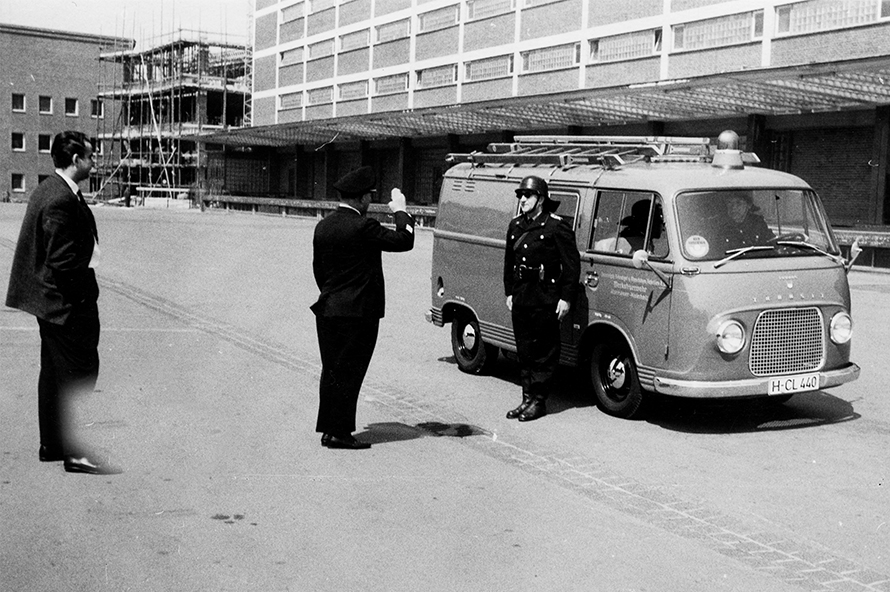
1880: We have a long tradition of safety: The VSM plant fire brigade
One of the greatest dangers for a manufacturing company has always been fire. Like many other companies, VSM therefore has its own fire brigade. Ours was founded on 1 July 1880 by the company founders Oppenheim and Seeligmann, making it one of the oldest fire brigades in Lower Saxony and Germany. It was initially made up of 14 employees and this number continued to grow steadily in the following years, to 37 employees in 1892. Initially, the water supply was the biggest problem, as the municipal water network did not yet reach as far as the plant premises. The only available source of water was a simple well. At that time, the main goal of the plant fire brigade was to immediately extinguish – or at least to contain their spread as far as possible.
The inadequate water supply also had direct dramatic consequences on the morning of 25 June 1884: A fire was detected too late and destroyed the affected factory building. The lack of water made it impossible to put out the fire. The plant fire brigade nevertheless prevented the flames from spreading to the rest of the plant by quickly building protective barriers.
In its early days, the fire brigade was not only limited to the plant, but also took part in operations in the district and neighbouring areas. Even today, on rare occasions it still attends large-scale operations of the municipal fire brigade.
In order to be able to react as quickly as possible in emergencies, emergency personnel were permanently located on the plant premises; even the night watchmen were trained as firefighters. During the Second World War, the plant fire brigade was successfully deployed several times after bombing raids, but was eventually pushed to its limits following the most severe and devastating attacks in 1945. Fortunately, VSM suffered no more major fires until 1985. In that year, a major fire occurred, resulting in the destruction of the thermal post-combustion system of a production line. Together with the aid of the professional fire brigade, the plant fire brigade prevented the fire from spreading.
Recently, the role of the fire brigade has changed somewhat. Due to greatly improved fire protection measures, fire fighting has become less of a requirement. In return, however, there has been an increase in technical assistance. For example, during the Christmas period in 1995, when a large amount of coolant leaked from a tank. The clean-up operation took up the whole of the holiday period and was done under extremely adverse conditions at temperatures as low as -20 degrees. Nevertheless, it was completed without the support of the municipal fire brigade.
Today, 144 years later, the plant fire brigade is still an institution at VSM. Its members not only have access to state-of-the-art equipment. Each member of the plant fire brigade has completed basic training and is qualified for the entry-level rank of firefighter at least. Modern technology and good training enable our plant fire brigade to create all the necessary conditions for us and our neighbours to feel as safe as possible around the clock.
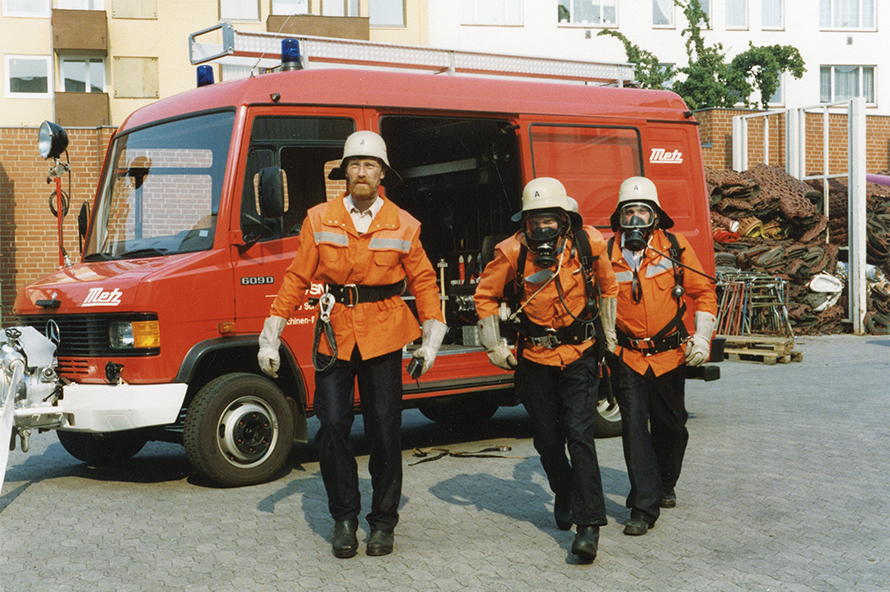
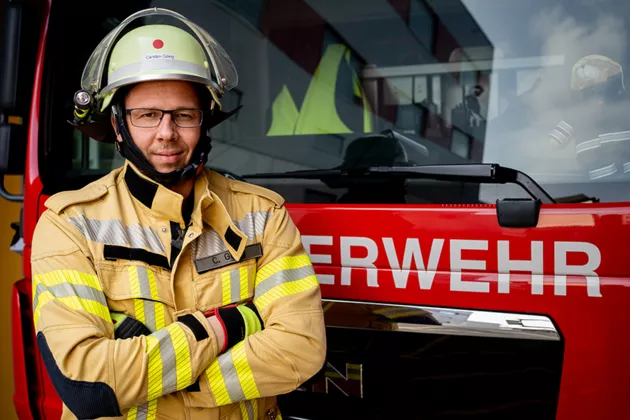
Discover VSM
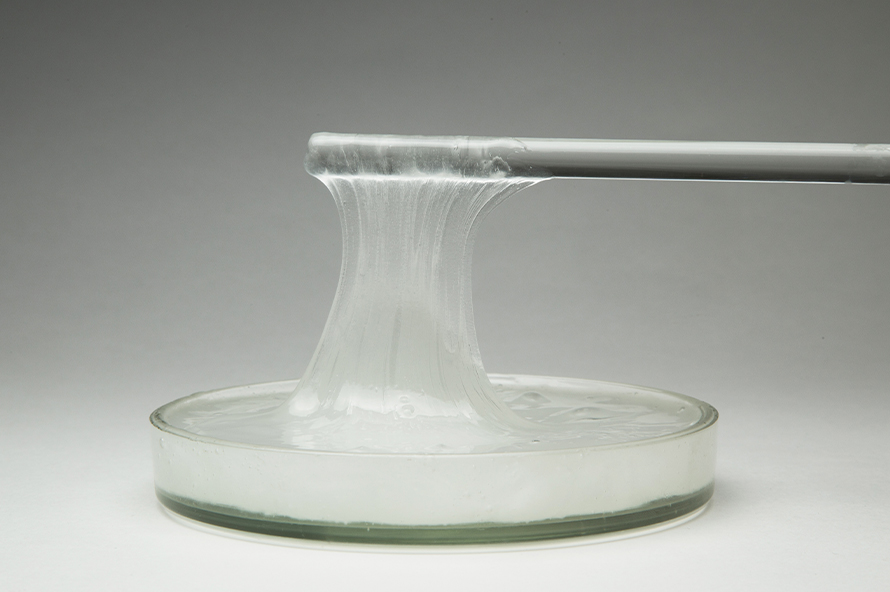
1888: The invention of wallpaper paste and VSM
What do discoloured wallpapers, a former VSM apprentice and the adhesion of the emery to the backing have in common? They all led to the invention of wallpaper paste.
During his apprenticeship at VSM, Ferdinand Sichel became aware of the complex processing of animal adhesives and bonding agents in the production of abrasives. He was already well aware of this problem from his parents’ company, a company for wallpaper and chalk paints. The animal-based raw materials had to be elaborately boiled and used quickly. They were also not waterproof.
These experiences prompted Ferdinand Sichel to invent new glues that were easier to work with. He developed Sichel paint adhesive using plant starch as a base. VSM also benefited from Sichel’s motivation to invent. Now we had access to new adhesives and bonding agents made from plant-based materials. They could also be processed cold, did not spoil and were quickly ready for use.
This is how wallpaper paste was invented in Hanover. An early technical innovation to which VSM also contributed.
Discover VSM
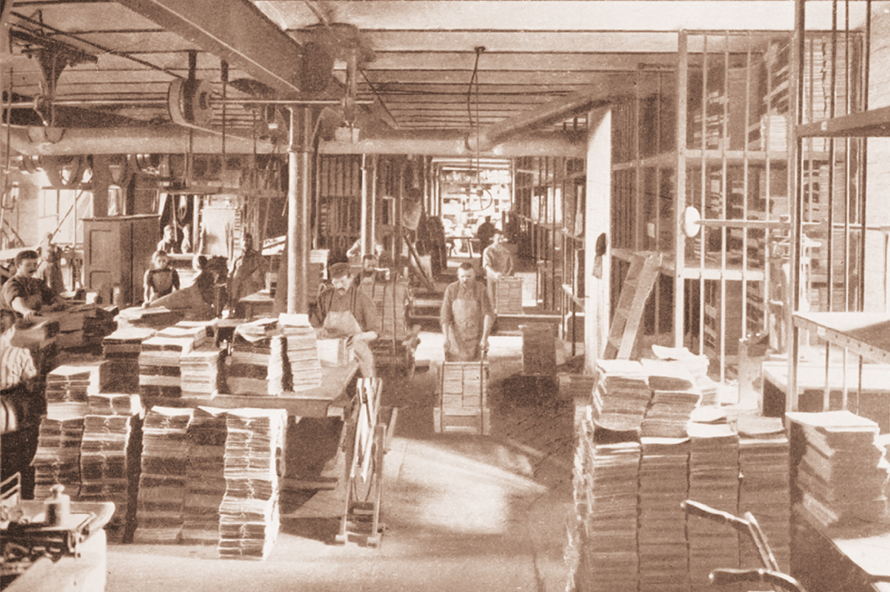
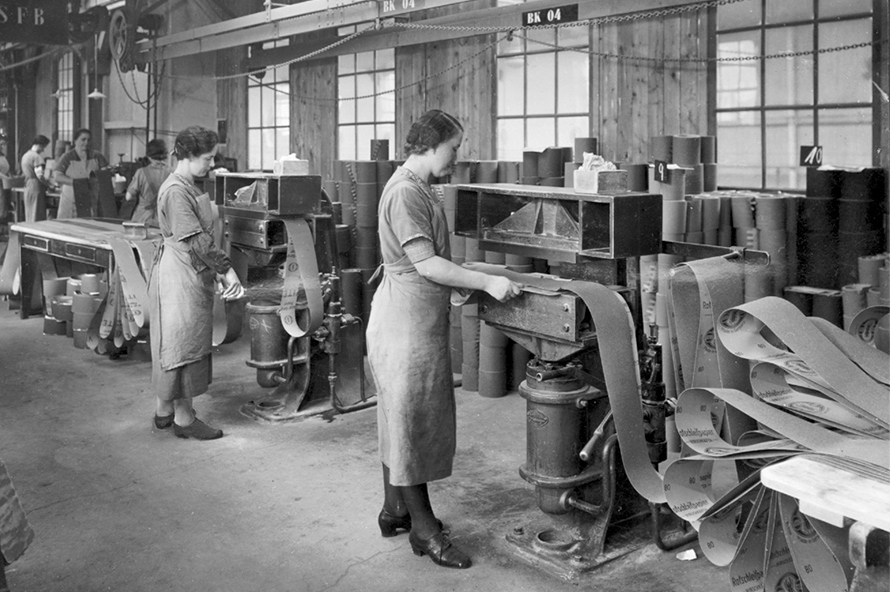
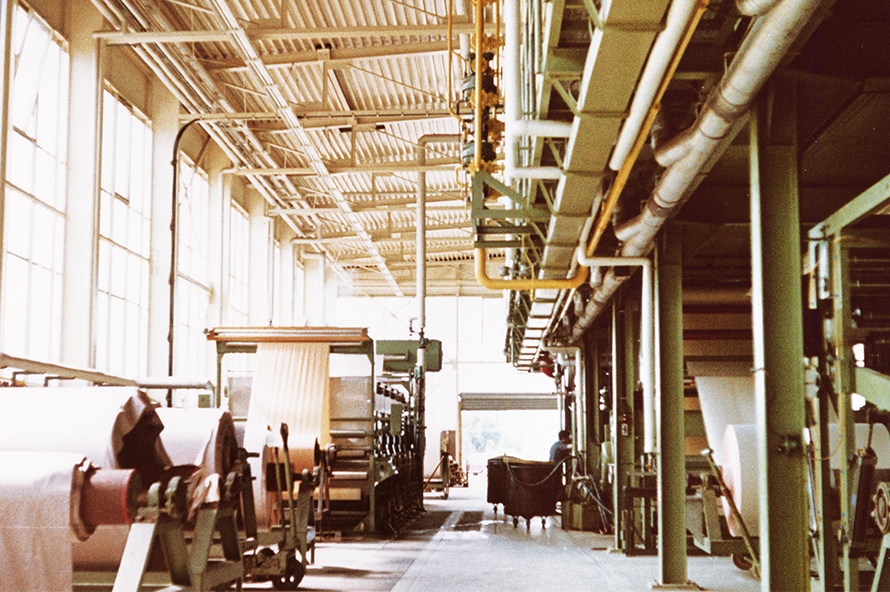
1930: Specialisation in coated abrasives
Our motto: Stay flexible at all times! After ceasing machine production as part of the global economic crisis, from 1929-30, VSM concentrated exclusively on the production of coated abrasives. A new finishing plant played a significant role at this time, as it was able to significantly increase product quality from 1932 onwards. This allowed us to produce cloth specifically for use as backings for flexible abrasives. At this time, these were referred to in Germany as Schleifleinen (abrasive linens). Today, backings made of cotton or polyester fabric are the current backings for our high-quality abrasives.
Our own finish means that we can still have a significant influence on the performance of our abrasives today. The production of our own backings from paper, cloth or vulcanised fibre is a crucial part of our vertically integrated production.
All in all, there is a wide range of flexible backings: from very flexible to very sturdy, we offer backings with the appropriate level of flexibility for every grinding application. As such, a wide range of abrasive products, including rolls, belts, discs and sheets & pads is produced.
Mix and structure are decisive, because there is the right composition for every material! VSM coated abrasives are made up of four or five components: Backing, base bond, abrasive grain, top size coat and an optional abrasive additional layer such as Top Size or ALU-X. The composition of the components has been tried and tested millions of times and ensures the desired properties of the abrasive – always optimised for specific applications.
The quick and precise adaptation of the abrasive to the material is one of the main advantages of coated abrasives compared to bonded abrasives, e.g. against grinding stones or grinding discs. This flexibility ultimately leads to higher workpiece quality – and at the same time increases profitability through more stock removal and shorter processing times.
In addition, coated abrasives have undeniable benefits for the user: They are easier to handle and ensure greater work safety: They provide protection for the user due to reduced vibration and noise.
With over 160 years of experience, our knowledge of abrasives is second to none.
Discover VSM
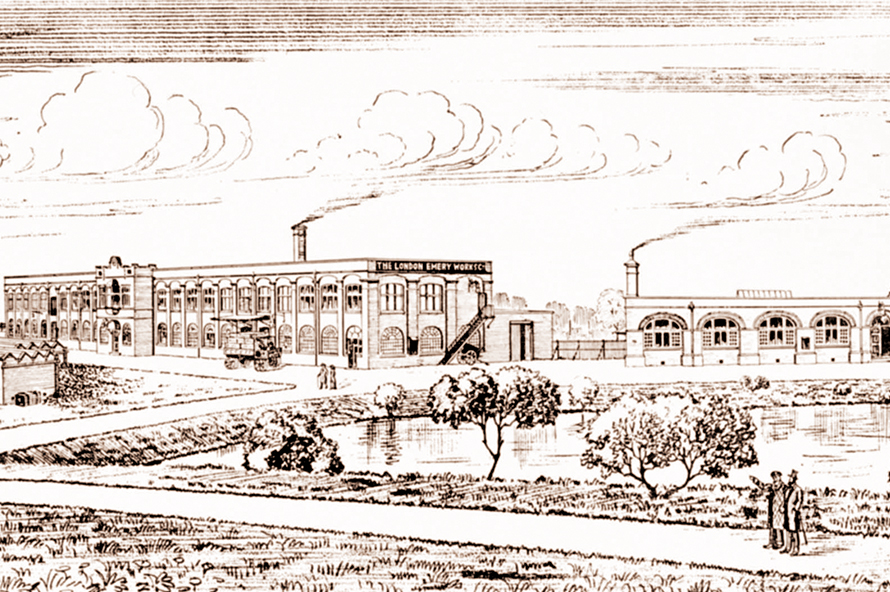
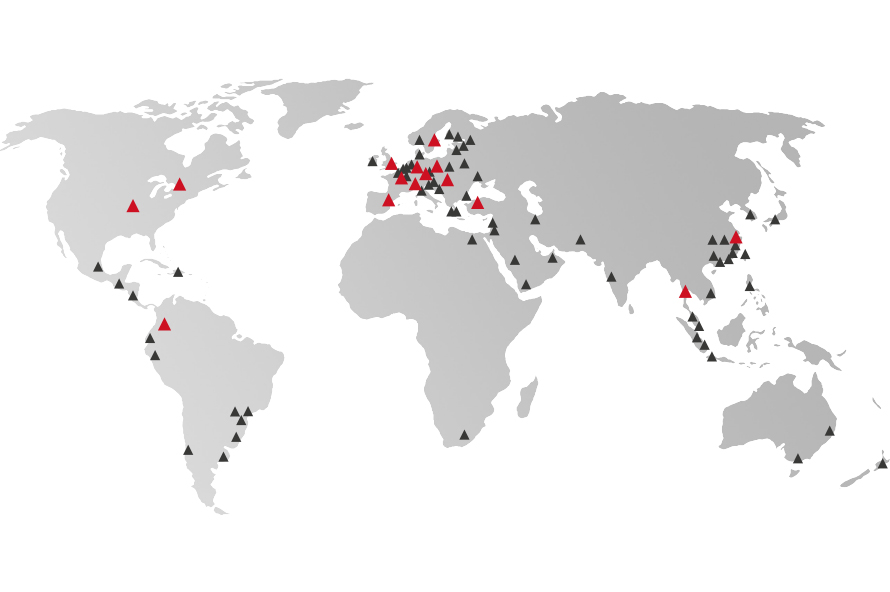
1955: VSM goes international
VSM’s high-quality abrasives attracted the attention of the industry in neighbouring countries at an early stage. As early as the 1890s, for example, VSM had an eye on the highly interesting English market and built a factory there based on the Hainholz model. The company was actually very successful in Great Britain with its own English brand “Atlas”, but the plant was lost in 1918 as a result of the First World War. But at the turn of the century, business was already booming in the rest of Europe. Early on, we had our own offices in Breslau, Brussels, Paris and Turin. But unfortunately, due to the two world wars, international business was also lost for the time being.
It was not until 1955 that the lost contacts to the United Kingdom could be re-established. With the establishment of the subsidiary VSM Abrasives Ltd., the internationalisation of VSM began in Great Britain. In 1974, the Spanish subsidiary VSM Vitex Abrasivo Iberica, S.A.U. was founded. And in 1978, the founding of VSM Abrasives Corporation in 1978 was a major milestone for VSM: The US subsidiary was able to successfully conquer the important US market for abrasives at the time.
Following the economic turbulence of the 1980s and strict modernisation measures, including new plants for weaving equipment and grain production, subsidiaries were founded in Canada (VSM Abrasives Canada Inc., 1992), Switzerland (Pferd-Vitex AG, 1994) and the complete acquisition of the Duna Vitex plant in Hungary (also 1994).
Since then, VSM has also been represented in Poland (Pferd-VSM Sp. Zoo, 1997), France (VSM Impavide S.A.S., 1998) and most recently in 2017 in Colombia (VSM Abrasivos Latinoamérica S.A.S.) with its own subsidiaries – and is close to its customers all around the world.
Today, VSM is active with subsidiaries or partners in more than 70 countries. A global network of VSM specialists provides expert advice wherever it is needed irrespective of whether your company is large or small.
Discover VSM
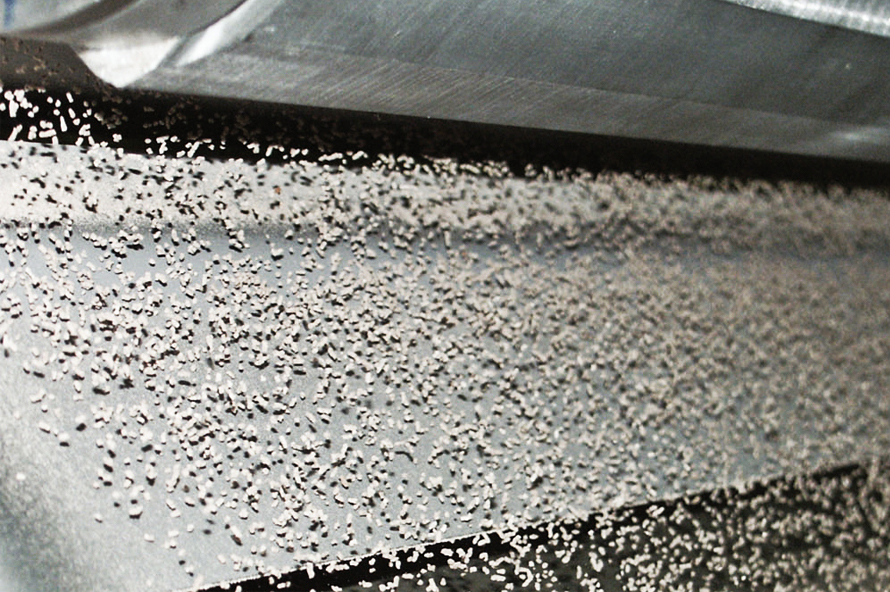
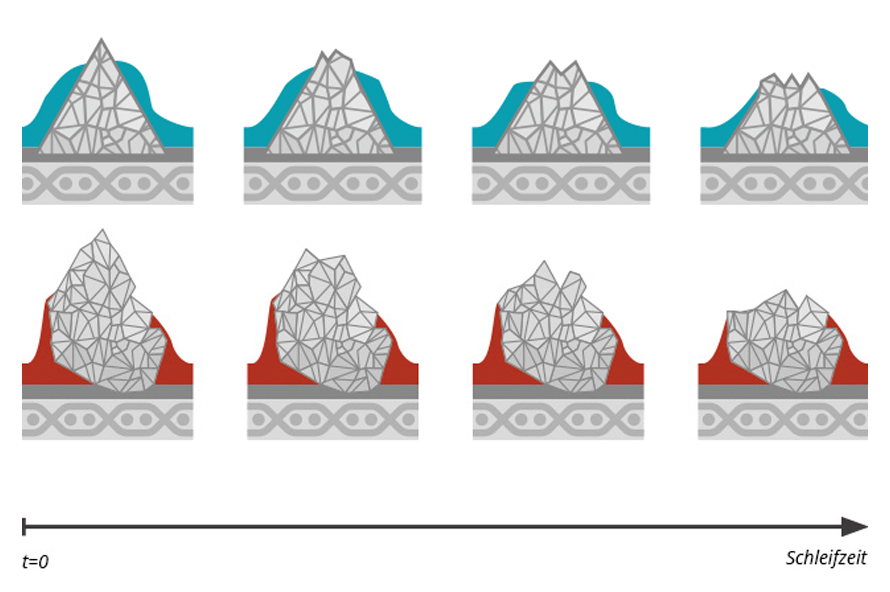
2004: Start of ceramic grain production
Hard-wearing: Our in-house developed and produced ceramic grain. The world of abrasives is always on the lookout for the best abrasive grain for specific applications. And when it comes to high stock removal, ceramic abrasive grains are clearly the first choice. This is because ceramic abrasive grains are particularly hard and tough.
What does this mean specifically? For example, during grinding, each individual grain is subjected to cutting forces that act like hammer blows. When machining hard metals such as titanium, the abrasive grain needs to withstand extreme loads over prolonged periods.
Another important aspect is the so-called self-sharpening effect. Our ceramic grain is produced in such a way that, thanks to its microcrystalline structure, it breaks down into very fine particles during grinding and thus always exposes new, sharp cutting edges. This guarantees consistently high stock removal – with maximum efficiency in the grinding process.
VSM ceramic grain has performed in this way for two decades now. Back in 2004, we started producing our own ceramic grain in Hanover, which quickly became the epitome of particularly high-performance abrasives under the name VSM CERAMICS.
Today, we are one of only a few ceramic grain manufacturers in the world. For twenty years, we have been working consistently to continue to be the ceramic grain champion. We therefore produce our ceramic grain exclusively in-house at the Hanover location with the highest quality standards. This allows us to have a crucial influence on the performance of our products – and to constantly further develop the sophisticated ceramic grain technology with our technical application expertise. For example, with VSM ACTIROX, which set new standards in 2018.
Discover VSM
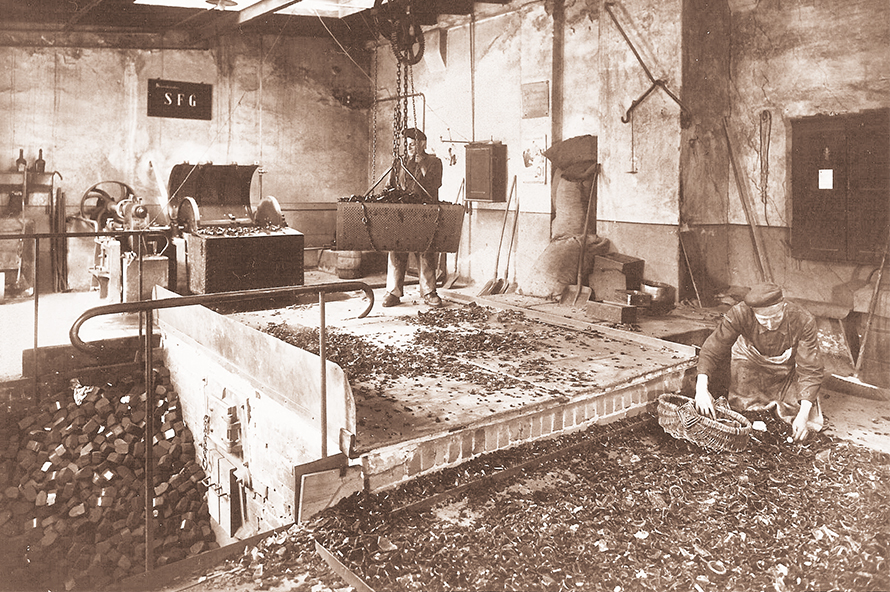
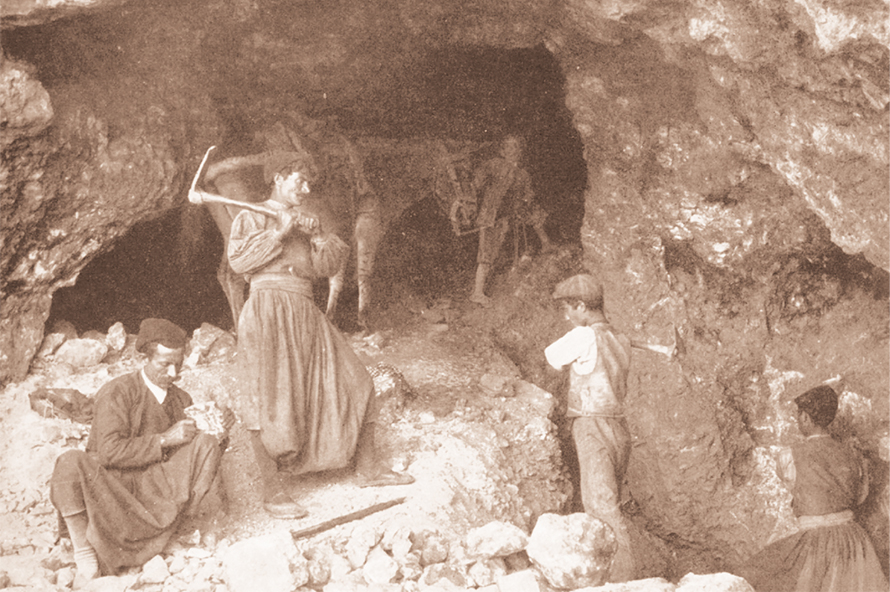
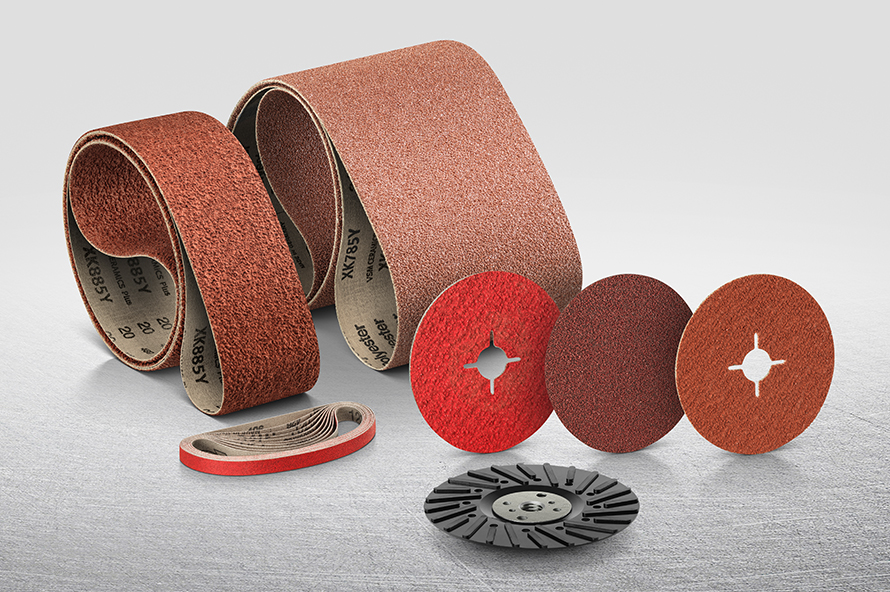
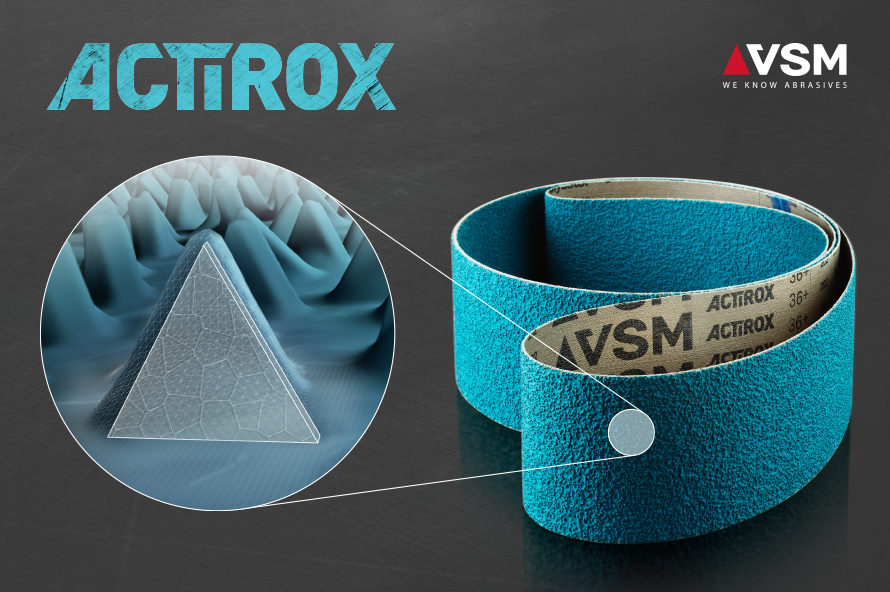
2018: From glass paper to high-end shaped ceramic grain
The first records of the use of sandpaper in England date back to the 18th century. Industrial use as a tool in the form of sandpaper, glass paper or flint paper began with the rapid ongoing industrialisation in Europe and America. Back then, the abrasive material was still attached to the paper backing by means of adhesive. These abrasives therefore performed poorly and they were primarily used for wood and other soft materials.
The first documented production of abrasives in Germany was set up by the company CF. Schröder in 1863. A little later, in May 1864, VSM also started, initially with the small-scale, manual production of glass and flint paper.
Industrialisation quickly placed the focus on new materials such as steel, for which glass and flint were not suitable. Emery was discovered as a more powerful alternative to glass. The hard rock did not wear out as quickly and delivered high grinding performance. It quickly became the company’s most important raw material. The emery paper was soon followed by other products such as emery cloth and emery discs.
Initially only dry abrasives were offered, but with the development of a waterproof ceramic-based bonding agent, products were also added that were suitable for wet grinding. By the turn of the century, natural abrasives such as emery were then increasingly replaced by synthetically produced abrasives such as aluminium oxide or zirconium alumina. Already at the beginning of the 20th century, VSM manufactured grinding wheels using the abrasives corundum and silicon carbide, which are still known and used today.
From the 1960s and 1970s onwards, a range of technical innovations enabled VSM to improve the quality of abrasives to a new level. Electrostatic coating, for example, which has been used since 1962, where abrasive grains are consistently applied with the tip uppermost on the backing, significantly increased the stock removal rate in one fell swoop.
1978 saw the next big step: VSM launched an abrasive with grain agglomerates. With the VSM COMPACTGRAIN long-term abrasive, new grains are released gradually and a new sharp grain can be ground again and again. This means that constant, reproducible surface values can be achieved with a uniform scratch pattern or gloss level, which is a particular requirement in the production of stainless steel fronts. To this day, VSM COMPACTGRAIN is still a bestseller. With more than 30 compact grain series, VSM has the widest range on the market today.
A particularly important milestone was the start of our own ceramic grain production in 2004 at the Hanover location. Like all VSM ceramic grain products, the first product, VSM CERAMICS, has a self-sharpening effect that ensures consistently high stock removal. From 2005 onwards, its success began in countless customer applications, and it delivered particularly impressive performance in the grinding of unalloyed steels and stainless steels. Customers achieved up to a 50 percent increase in service life compared to other ceramic grain abrasives. A new era of stock removal had begun.
In 2007, we launched our VSM Diamond and CBN abrasives. These were specially developed for machining extremely hard materials such as tungsten carbide, titanium carbide, chromium oxide, glass, ceramic, GRP, Kevlar and natural stone.
In 2018, VSM took ceramic grain development to the next level with its geometrically shaped VSM ACTIROX. It achieves even greater stock removal – maximum stock removal, as we rightly say – with long service life and an aggressive, cool cut. With ACTIROX, we are one of the few manufacturers worldwide of geometrically shaped ceramic grains.
In the same year, VSM launched an abrasive innovation that enabled grinding and polishing in one step. The “coated” ILUMERON goes one step further than our previous long-term abrasives, as it enables a particularly high gloss level. The extremely tight tolerances in the ground surfaces impressed users all over the world.
In 2023, a special development for the grinding of aluminium and non-ferrous metals also came onto the market: VSM ALU-X significantly reduces chip adhesion and thus reduces tool changes. The increase in performance enables faster machining and lowers the process costs. Grease-free and oil-free grinding keeps the workplace clean.
What does the future hold? This is an exciting question that we would like to answer. We are continuing to work hard to offer our customers the best and most innovative abrasive solutions.